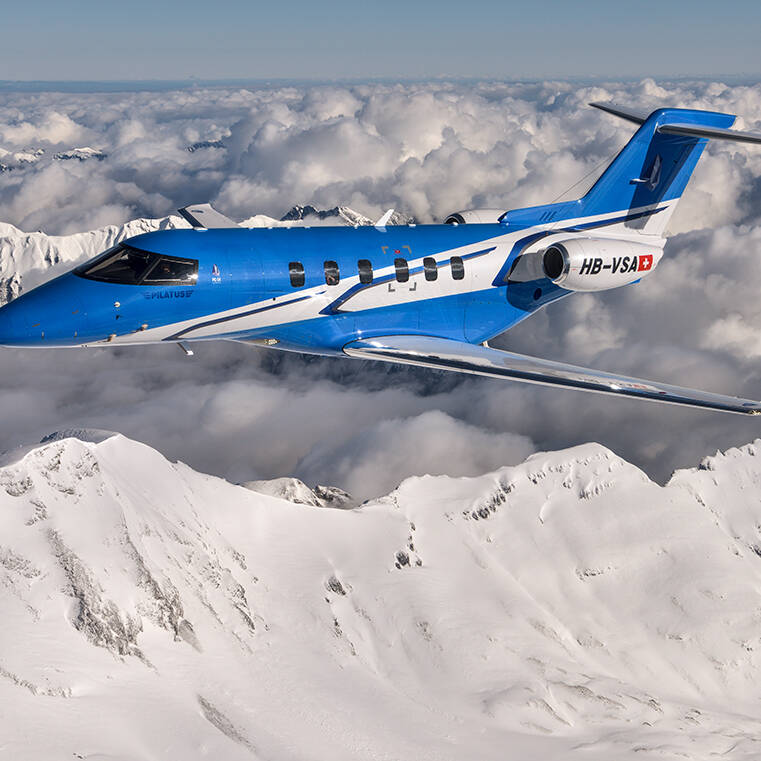
Con i materiali compositi verso nuovi orizzonti
I nuovi business jet PC-24 di Pilatus, con il loro peso di cinque tonnellate, sono così leggeri che possono decollare e atterrare anche su piste in erba corte. La riduzione del peso si ottiene grazie all'impiego di componenti in fibre di carbonio e di vetro. Per il loro taglio, Pilatus si basa sulla modernissima tecnologia di taglio di Zünd.
Ore 08:10, Fano, Italia centrale, il PC-24 si prepara all'atterraggio all'aeroporto di Fano. L'incontro di lavoro, distante due chilometri da Fano, inizia alle 9. È uno scenario inconsueto: il velivolo è un business jet PC-24 nuovo di zecca della Pilatus Flugzeugwerke AG e la pista di atterraggio è non consolidata e accidentata e misura solo 1300 metri. Solitamente, i business jet di questa classe atterrano a Rimini - ad un'ora e mezza di auto: la donna d'affari avrebbe avuto davanti a sé ancora un lungo tragitto in automobile.
Finora gli atterragi su piste in erba e ghiaia corte e non consolidate erano riservati a turboelica. Da poco è possibile anche con uno dei nuovi PC-24. Il business jet può decollare già dopo 890 m e per l'atterraggio bastano 720 m. Questo è dovuto al suo peso di base di sole 5,3 tonnellate. Questo peso ridotto è dovuto in gran parte al fatto che nel nuovo PC-24 vengono montati numerosi componenti in fibre di carbonio o di vetro. Per il taglio, Pilatus da anni utilizza la tecnologia di taglio del San Gallo Rheintal. Nel 2018 Pilatus ha optato nuovamente per un cutter digitale Zünd altamente automatizzato.
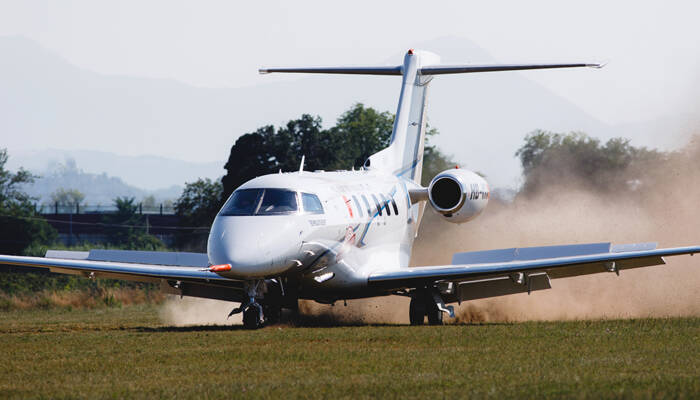
Come si costruisce un aeroplano?
Patrick Rohrer, capoprogetto Approvvigionamento impianti presso Pilatus sa cosa occorre per costruire aeroplani efficienti: "Il know how della sede di produzione, il made in Swiss, questo è il primo aspetto. È almeno altrettanto importante disporre di celle di produzione altamente moderne, equipaggiate con tecnologia di punto" A questo proposito al centro si mettono le riduzione permanente dei costi, l'ottimizzazione dell'efficienza e la capacità di poter mettere in pratica moderne tecnologie di fabbricazione.
Nel 1959 era del tutto diverso. Allora il PC-6 Porter decollò per la prima volta dalla pista di Stans. Un velivolo universale robusto con struttura in metallo pieno, chiamato anche "Jeep con le ali" e versatile come un coltellino svizzero. I PC-6 erano assemblati esclusivamente a mano. I dipendenti dovevano essere molto esperti e le tolleranze erano più ampie di oggi. Il più recente tipo di velivolo, il PC.24, si compone di innumerevoli pezzi, molti dei quali fresati con tolleranze nell'ordine dei Mµ. Oggi l'assemblaggio, effettuato soltanto con le tecnologie di fabbricazione più moderne, è molto più rapido.
Da quest'anno il PC-6 non viene più costruito: dopo la costruzione di 500 esemplari si è conclusa la sua incredibile storia. Il suo successore, il PC-12, dal 1994 venduto oltre 1650 volte in tutto il mondo, è oggi il turboelica monomotore più popolare sul mercato.
Nelle costruzioni aeronatiche, l'impiego di pezzi in fibre di carbonio è precoce. Anche nel PC-6 i primi componenti in fibra di vetro e di carbonio sono stati prodotti nel procedimento di laminazione manuale, per quanto ancora in quantità comprensibili.
Nelle costruzioni aeronautiche quasi tutto ruota attorno alla riduzione del peso. Per questa ragione, un numero sempre maggior di parti viene fabbricato in fibre di carbonio e in fibre di vetro. Il loro principale vantaggio è la rigidità elevata e la durezza nonché la resistenza all'usura. La sfida è trovare l'equilibrio tra peso, stabilità e costi. "Si aggiungono fattori come carico utile e spazio utile, che devono essere i più grandi possibile." Gli elementi portanti costruiti da Pilatus non vengono ancora prodotti in fibre di carbonio, ma nell'area Ricerca e Sviluppo ci stanno lavorando intensamente. Nel PC-24 i materiali compositi vengono utilizzati principalmente per i rivestimenti interni ed esterni. Anche le ali e i rivestimenti del propulsore sono fabbricati in fibre di carbonio, così come i portelloni del carrello, i canali dell'aria, vari tubi, le coperture e i bordi di uscita delle ali.

Prepreg, il futuro delle costruzioni aeronautiche
Il punto di partenza di questi componenti di aerei sono i tessuti preimpregnanti, i cosiddetti prepreg: delle fibre continue vengono impregnate e poi consolidate con temperatura e pressione. I prepreg hanno resistenza e rigidità elevate, sono resistenti alla fatica e all'usura, difficilmente infiammabili e non si lasciano influenzare dall'ambiente circostante.
I prepreg vengono consegnati in rotoli mediante camion refrigerante e immagazzinati a -19 gradi nel congelatore. Per raggiungere la temperatura ambiente entro il momento del taglio, vengono prelevati dal frigorifero la sera precedente. Il materiale può rimanere a temperatura ambiente da cinque a 20 giorni: trascorso tale periodo di tempo, la resina reagirà e indurirà. Ogni giorno Pilatus lavora circa cinque rotoli da 90m2 circa, all'incirca 90'000 m2 all'anno. Il consumo aumenta continuamente: attualmente più della metà dei nuovi componenti in fibra di carbonio e in fibra di vetro fabbricati nel reparto plastica vengono montati sul nuovo PC-24. Per il taglio delle pellicole di prepreg, Pilatus utilizza da oltre 15 anni la tecnologia di taglio digitale di Zünd. Oggi come sempre, il cutter della serie PN è affidabile. Con l'aumento della richiesta di componenti di fibre di carbonio, ha però raggiunto la sua capacità limite. Così, dal 2019 un cutter G3 L-2500 Zünd altamente moderno taglia in modo completamente automatizzato i singoli strati per i rispettivi componenti e li dota di iscrizioni inline con un modulo a getto di inchiostro integrato.
Dopo il taglio, i pezzi tagliati vengono raccolti in modo da formare un kit e immagazzinati nella cella frigorifera fino all'utilizzo successivo. A seconda dei requisiti in termini di rigidità e spessore, un componente può quindi essere composto da fino 350 strati.
Per i pezzi tagliati e i relativi singoli strati, per cui non sono disponibili dati DXF, viene utilizzata la cosiddetta tavoletta grafica: una tavola di digitalizzazione. In questo modo, basta alloggiare i modelli dei componenti sul tavolo e digitalizzarli. Con la tavoletta grafica è possibile adattare e digitalizzare in tutta semplicità anche le minime modifiche dei componenti approvate dal reparto di Engineering.
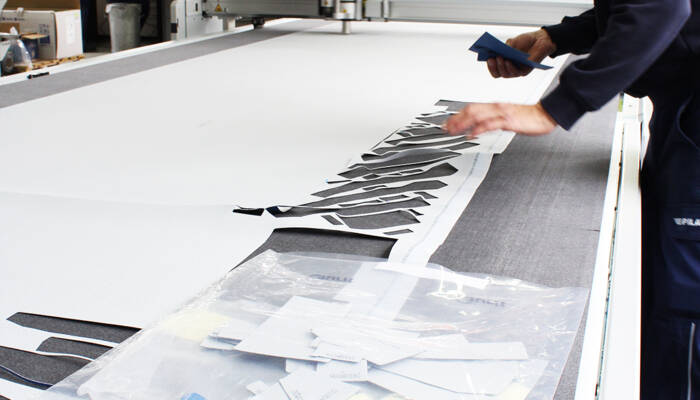
L'efficienza dei materiali è una tematica costante
Anche l'ottimizzazione permanente dell'efficienza contribuisce al successo del Pilatus, spiega Patrick Rohrer. "Quando si usano materiali costosi, come le fibre di carbonio o di vetro, l'efficienza dei materiali e la loro ottimizzazione sono tematiche costanti. Lavoriamo incessantemente per aumentare il livello di utilizzo, riducendo di conseguenza anche gli scarti. Scarti che purtroppo sono poco riutilizzabili". Intanto, la quota di scarti è passata dal 30 all'attuale 20%. In questo contesto, ricopre un ruolo importante il nesting ad alta efficienza del software Zünd Cut Center – ZCC. Da un lato i pezzi tagliati vengono annidati in modo statico. Ciò significa che viene effettuato il nesting di un articolo, nello specifico dei suoi singoli strati, nella quantità del singolo ordine. "Il nesting dinamico, ovvero l'annidamento di diversi ordini in un job di taglio, viene utilizzato ogni qualvolta lo si ritenga opportuno". Ciò aumenta ulteriormente il livello di utilizzazione del materiale grezzo.
L'intero pacchetto è unico nel suo genere
Zünd si è nuovamente aggiudicata la modernizzazione del parco macchine nel reparto plastica: ciò è da ricondurre, tra l'altro, a certe somiglianze tra le due aziende, e al fatto che, come spiega Patrick Rohrer, Zünd offre una soluzione complessiva modulare unica. Come Pilatus, anche Zünd si rispecchia nei valori produttivi della Svizzera: qui sviluppa e produce soluzioni hightech per il mercato mondiale, servendosi delle più moderne tecnologie e di specialisti altamente qualificati. Rohrer conclude sottolineando che anche le brevi distanze sono un fattore importante per l'efficacia della collaborazione. "Possiamo contare su 15 anni di esperienza con la tecnologia di taglio di Zünd: ciò ha senza dubbio il suo peso. Zünd offre soluzioni aperte e modulari con contratti di assistenza opzionali e un software estremamente affidabile senza che siano necessari continui aggiornamenti. Questo è esattamente quello che intendiano quando parliamo di vantaggi per il cliente". Zünd dà immenso valore all'assistenza clienti, un ulteriore punto in comune tra le due aziende.
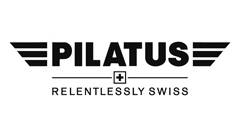