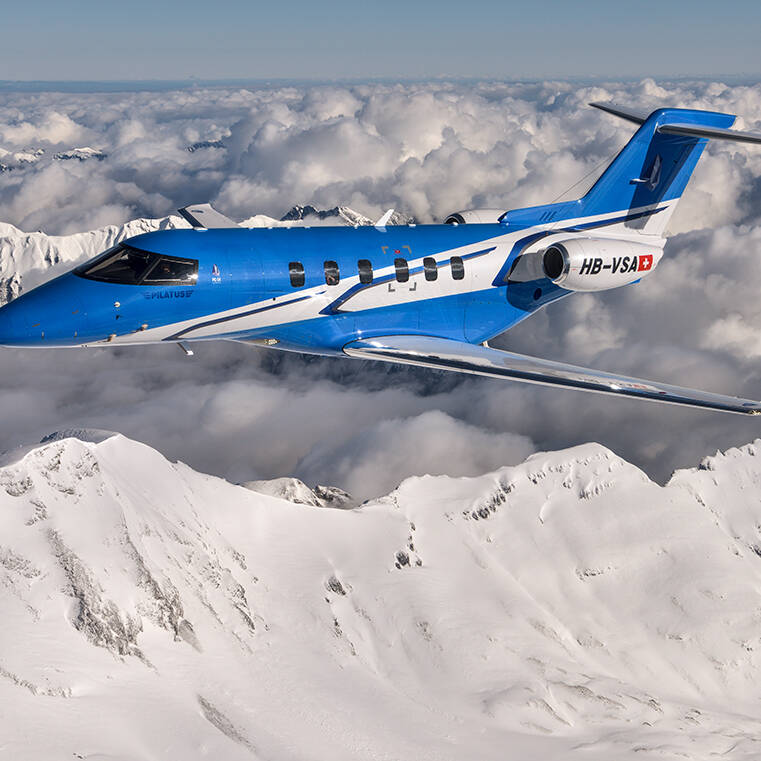
Avec des composites vers de nouveaux horizons
Les nouveaux jets d’affaires Pilatus PC-24 pèsent cinq tonnes et sont assez légers pour décoller et atterrir sur des pistes engazonnées. Son faible poids est obtenu grâce à l'utilisation de composants en fibres de carbone et de verre. Pour ses découpes, Pilatus s'appuie sur la technologie de coupe ultramoderne de Zünd.
08 h10, Fano, Italie centrale, le PC-24 se prépare pour l’atterrissage à l’aéroport de Fano. La réunion d’affaires à Fano, à deux kilomètres de là, commence à 9 heures. Il s’agit à cet égard d’une situation peu familière puisque cet avion est un tout nouvel avion d’affaires PC-24 Pilatus et que la piste n’est pas pavée et cahoteuse et ne mesure que 1 300 mètres. En règle générale, les jets d’affaires de cette classe atterrissent à Rimini, à une heure et demie de voiture, et la femme d’affaires aurait eu à conduire un long trajet après l’atterrissage.
Les atterrissages sur des routes courtes et non goudronnée en herbe et en gravier étaient auparavant réservés aux avions à turbopropulseurs. Récemment, cela est également possible pour les tout nouveaux PC-24. L'avion d'affaire peut décoller en seulement 890 mètres et atterrir en 720 mètres. Cela est dû à son poids de base de seulement 5,3 tonnes. Une part importante de ce faible poids réside dans l'utilisation de nombreux composants en fibres de carbone ou de verre dans le nouveau PC-24. Pour la découpe, Pilatus s'appuie depuis des années sur la technologie de coupe de la vallée du Rhin St-Gallois. En 2018, Pilatus a de nouveau opté pour un Cutter Zünd numérique hautement automatisé.
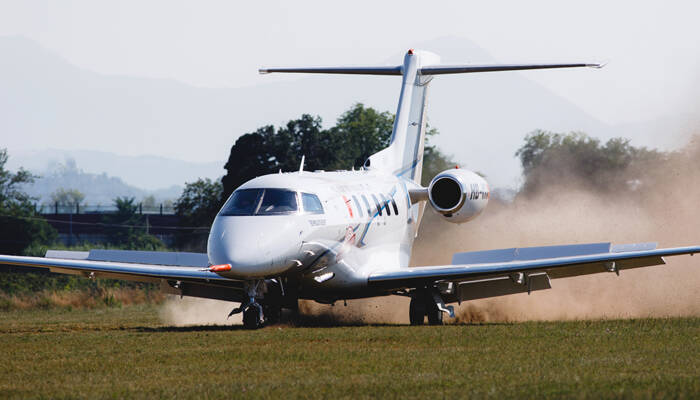
Comment construis-tu un avion ?
Patrick Rohrer, chef de projet Approvisionnement des systèmes chez Pilatus, sait ce qui est nécessaire pour construire des avions performants : « L'engagement envers le site de production, la Swissness, est une chose. Des cellules de production modernes, dotées de technologies de pointe, sont au moins aussi importantes ». L'accent est mis ici sur la réduction permanente des coûts, l'optimisation de l'efficacité et la capacité à mettre en œuvre des technologies de production modernes.
C'était cependant différent en 1959. À cette époque où le PC-6 Porter décolla pour la première fois de l'aérodrome de Stans. Un avion universel tout en métal robuste, certains l'ont également appelé « Jeep volante », polyvalent comme un couteau militaire suisse. Les PC-6 ont été assemblés exclusivement à la main. Les employés devaient avoir une expérience appropriée et les tolérances étaient plus grandes qu'aujourd'hui. Le dernier type d'avion, le PC-24, est composé d'un nombre incalculable de pièces, pour la plupart usinées, avec des tolérances en µm. L'assemblage se fait beaucoup plus rapidement aujourd'hui, ce qui n'est possible que grâce aux technologies de production les plus modernes.
Depuis cette année, le PC-6 n'est plus construit, sa Success Story se termine après la production du 500ème exemplaire. Le successeur, le PC-12, vendu plus de 1650 fois dans le monde entier depuis 1994, est l'avion monomoteur à turbopropulseur le plus populaire sur le marché à ce jour.
Les premières pièces en fibre de carbone ont été utilisées très tôt dans l'industrie aéronautique. Les premiers composants en PRV et de PRFC ont également été produits à la main dans du PC-6, en quantités toutefois raisonnables.
Presque tout est axé sur la réduction de poids dans l’industrie aéronautique. De ce fait, de plus en plus de pièces sont fabriquées à partir de fibres de carbone et de verre. Leur gros avantage est leur grande rigidité et dureté, ainsi que leur bonne résistance à l'usure. Le défi consiste à trouver un équilibre entre poids, stabilité et coût. « En outre, certains facteurs, tels que la charge utile et l'espace de travail, doivent être aussi importants que possible ». Chez Pilatus, aucune pièce porteuse n'est fabriquée en PRFC, mais des travaux intensifs sont en cours au département de Recherche et Développement. Le PC-24 applique des composites principalement pour le revêtement intérieur et extérieur. Les capots du groupe moteur et les extrémités des ailes sont en fibre de carbone, tout comme les portes du châssis, les conduits d’air, divers tuyaux, capots ou les bords inférieurs des ailes.

Les pré-imprégnés, l'avenir de la construction aéronautique
La base de ces pièces d'avion est constitué de tissus pré-imprégnés, appelés pré-imprégnés ou prépegs. Les fibres continues sont imprégnées et consolidées sous pression et à haute température. Les préi-mprégnés ont une résistance et une rigidité élevées, sont résistants à la fatigue et à l'usure, sont ignifuges et résistent aux influences de l'environnement.
Les pré-imprégnés sont livrés en rouleaux par camion frigorifique et stockés à -19 degrés dans un congélateur. Pour les amener à la température ambiante, ils sont sortis du congélateur la nuit précédente. Le matériau peut rester pendant cinq à vingts jours à température ambiante avant que la résine ne réagisse et ne durcisse. Pilatus traite environ cinq rouleaux d'environ 90 m2 par jour, soit environ 90 000 m2 par an. Et sa consommation augmente constamment ; aujourd'hui, plus de la moitié des composants en PRFC et PRV produits dans le département des plastiques sont installés dans le nouveau PC-24. Pour couper des films pré-imprégnés, Pilatus s’appuie sur la technologie de découpe numérique de Zünd depuis plus de 15 ans. Le Cutter de la série PN continue à exécuter ses tâches de manière fiable. Cependant, avec la demande croissante de composants en fibre de carbone, la limite de capacité a été atteinte. Depuis 2019, par exemple, un Cutter G3 L-2500 Zünd, à la pointe de la technologie, découpe chaque couche des composants de manière largement automatique et les marque en ligne à l'aide d'un module à jet d'encre intégré.
Après la coupe, les pièces découpées sont assemblées dans un kit et stockées dans le congélateur pour une utilisation ultérieure. Un composant peut comporter jusqu'à 350 couches, en fonction des exigences de rigidité et de résistance.
Pour les pièces coupées et chaque de leurs couches pour lesquelles aucune donnée DXF n'est disponible, il est possible d'utiliser le numériseur, un tableau de numérisation. Les modèles de composants peuvent donc être facilement enregistrés et numérisés sur la table. Même les modifications mineures apportées aux composants validées par l'ingénierie peuvent être facilement adaptées et numérisées avec le numériseur.
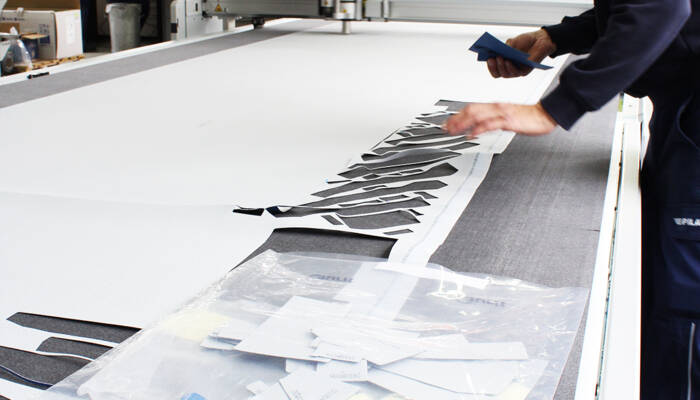
L'efficacité matérielle est une problématique constante
L’optimisation permanente de l’efficacité contribue également au succès de Pilatus, explique Patrick Rohrer. « Lorsqu'il s'agit de matériaux coûteux, tels que les fibres de carbone ou de verre, l'efficacité et l'optimisation des matériaux sont une problématique constante. Nous travaillons constamment pour augmenter le degré d'utilisation et réduire ainsi les déchets. Déchets qui peuvent encore difficilement être recyclés ». Dans l'intervalle, le taux de déchets a été réduit de 30 à 20 % aujourd'hui. L'imbrication à haute efficacité via le logiciel Zünd Cut Center, ZCC, joue ici un rôle important. D'une part, les pièces découpées sont imbriquées de manière statique. C'est-à-dire qu'un article ou ses couches sont imbriquées dans un numéro de tâche. « L'imbrication dynamique, c'est-à-dire l'imbrication de plusieurs tâches dans un travail de coupe, est également toujours possible, le cas échéant. » Cela augmente encore le taux d'utilisation de la matière première.
Le paquet complet est unique
Le fait que Zünd ait remporté l'offre de modernisation des machines du département plasturgie est parfois dû à certaines similitudes entre les deux sociétés. Et que Zünd propose une solution globale modulaire unique, comme le déclare Patrick Rohrer. Tout comme Pilatus, Zünd s’engage également à produire et développer en Suisse des solutions de haute technologie pour les marchés mondiaux, avec une technologie de pointe et des spécialistes hautement qualifiés. Donc, la proximité est un facteur important, qui rend la coopération fructueuse, conclut Rohrer de manière concluante. « Nous avons 15 ans d'expérience avec la technologie de découpe Zünd, ça compte. Zünd propose des solutions ouvertes et modulaires avec des contrats de service optionnels et un logiciel extrêmement fiable sans mises à jour de courte durée. C'est exactement ce que nous entendons par avantage client réel ». Zünd attache une grande importance à la qualité du service à la clientèle, autre point commun des deux entreprises.
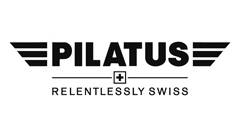