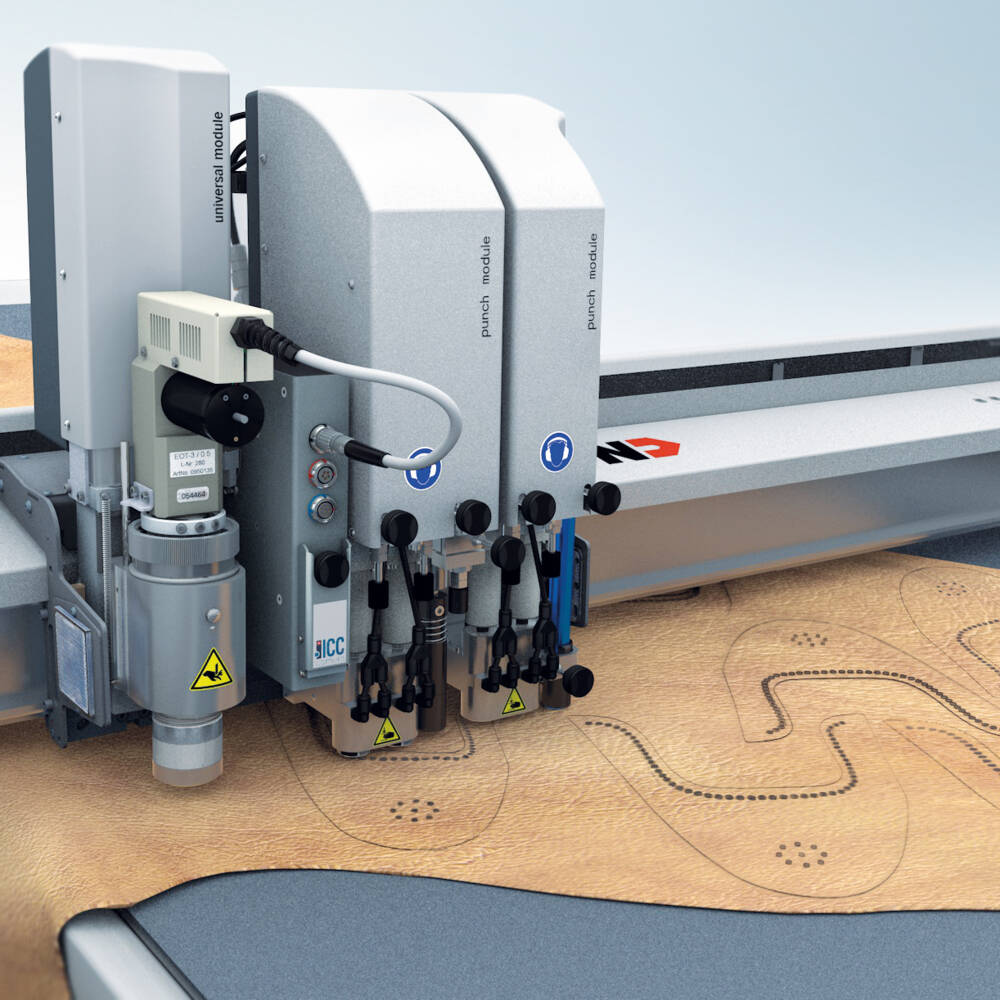
Über sparsame Deutsche und die digitalisierte Schuhproduktion
Die Deutschen sind ein sparsames Volk. Nicht mehr als ein Klischee zwar, aber eines mit einem wahren Kern. Das Beispiel des deutschen Schuhfabrikanten Berkemann zeigt, dass Sparsamkeit in Kombination mit Fachwissen und Kompetenz in der Digitalisierung von Prozessen an die Spitze deutscher Schuhhersteller führen kann. Das Unternehmen hat ihre Zuschnittabteilungen konsequent digitalisiert und setzt dabei auf digitale Schneidtechnologie und Software von Zünd.
Seit über 130 Jahren fertigt Berkemann Komfortschuhe. Komfort steht für bequeme Passformen, hochwertige Materialien, Langlebigkeit und Nachhaltigkeit. Komfort bedeutet für Christoph Kannengiesser, den Leiter technische Projekte Schuh aber auch, dass man «einander zuhört, die Kundenbedürfnisse kennt, sich jeden Tag aufs Neue fragt, wo und wie man sich weiter verbessern kann. Kannengiesser ist die führende Kraft hinter der konsequenten Digitalisierung der Schuhherstellung, insbesondere mit hochmoderner Erfassungs-, Qualifizierungs- und Zuschnitttechnologie von Zünd. Dazu später mehr.
Berkemann ist ein traditionsreiches Haus. 1885 in Hamburg von Heinrich Adolf Berkemann gegründet, beschäftigt die Berkemann-Gruppe heute an ihren Produktions- und Verwaltungsstandorten in Deutschland, Kroatien, Tschechien und Ungarn rund 1’000 Mitarbeitende.
Allein in Ungarn betreibt Berkemann mittlerweile vier Produktionsstandorte: «In Ungarn, dem Land der Schuhmacher und der Budapester-Schuhe, fertigen wir mit handwerklichen Geschick und Know-how unserer Fachkräfte Komfortschuhe. Dabei erlaubt uns die Produktion mitten in Europa, schnell auf Marktanforderungen zu reagieren, unsere Lieferwege kurz und die Lieferketten transparent zu halten», erklärte es Geschäftsführer Thomas Bauerfeind kürzlich an einer Jubiläumsveranstaltung zum 25-jährigen Bestehen von Berkemann Ungarn.
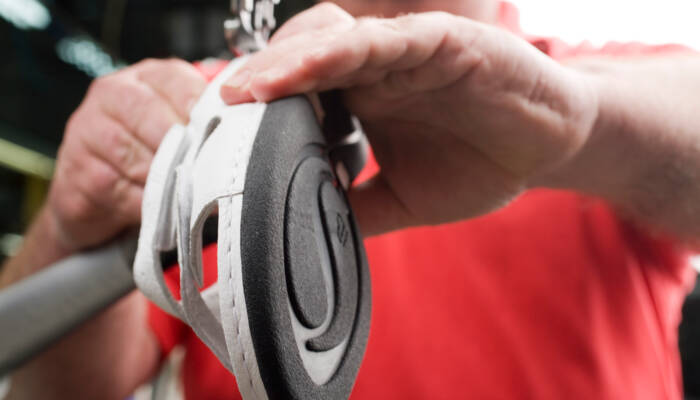
(Wirtschaftlich) nachhaltig im Zuschnitt
Nachhaltigkeit ist ein zentrales Thema bei Berkemann und zieht sich als roter Faden durch die Produktion. Doch am Ende des Tages muss sie wirtschaftlich sinnvoll sein. Dazu Christoph Kannengiesser, Leiter technische Projekte: «Sie sprechen einen zentralen Punkt unseres Investitionsprojektes in Ungarn an. Im Rahmen der Digitalisierung des Zuschnitts in unserem Werk im ungarischen Kiskunfélegyháza war die Substitution des bis anhin für die Stanzformen verwendeten Bandstahls ein zentraler Punkt». Ein noch wichtigeres Thema in der Evaluationsphase war allerdings die Digitalisierung der Lederqualifizierung. Denn erst die digitale Bewertung und Vermessung der Lederhäute macht die folgenden Prozessschritte wiederholbar.
Genestet wird bei Berkemann schon lange. Ein weiteres Entscheidungskriterium war denn auch, dass das Nesting mit der neuen Mind-Software mindestens ebenbürtig sein musste, gerne auch besser. «In den meisten Fällen sind wir mit dem Mind-Nesting heute effizienter unterwegs. Wir können die Schnittteile auf eine Haut, die zuvor digital erfasst und qualitativ bewertet worden ist, effektiver verschachteln», führt Kannengiesser aus.
Digitale Inspektion und virtuelle Markierung – MindCUT Diva
Geht es um digitalisierte Bewertung der Lederhäute, kommt Kannengiesser ins Schwärmen. Berkemann hat in zwei MindCut Diva investiert. Diva steht für Digital Inspection and Virtual Annotation. Mitarbeiterinnen, die nach dem Ersatz der Schwenkarmstanzen durch Zünd Cutter anderweitig eingesetzt werden mussten, qualifizieren heute an den Divas eine ganze Haut in unter fünf Minuten. «Ich brauche auch an einer Diva qualifiziertes Personal, das unsere Kollektion kennt, das sich bei Lederqualitäten oder Zugrichtungen auskennt. Diese Leute wissen genau, welches Schnittteil sie wie tief in die Fläme platzieren können».
Auftragsbezogen prüfen, ob die Lederlieferung in Qualität und Menge auch dem entspricht, was geordert wurde? Was bisher kaum möglich war, ist laut Kannengiesser zur Routine geworden: «Ich kann mit der Diva jede Haut fotooptisch dokumentieren und ausmessen. Und habe damit eine elegante Lösung. um etwaigen Unterlieferungen vorzubeugen. Wenn wir 500 Meter bestellen, möchten wir gerne 505 Meter geliefert bekommen, aber bitte nicht 490. Und wenn ich erste Wahl ordere, möchte ich auch nur für erste Wahl bezahlen. Mit MindCut Diva haben wir ein ziemlich mächtiges Werkzeug im Einsatz. Damit sind wir deutlich effizienter unterwegs und wir können gleichzeitig unseren Lederlieferanten ziemlich genau auf die Finger schauen.»
Von der Handarbeit zur digitalen Produktion
Mit den digitalen Lösungen gelingt es Berkemann, die junge computeraffine Generation wieder mehr für die Arbeit in der Zuschneiderei zu begeistern. Sie arbeiten lieber an computergesteuerten modernen Produktionssystemen als an angestaubten Schwenkarmstanzen. Für das Personal, das bis anhin an den Schwenkarmstanzen gearbeitet hatte, war die Umstellung auf einen digitalisierten Zuschnitt eine grosse Umstellung. «Wir haben die Leute an die Hand genommen und ihnen ihre Aufgaben Schritt für Schritt nähergebracht. In diesem Prozess sind wir von Zünd hervorragend unterstützt worden».
Berkemann setzt in ihren Produktionsstätten in Ungarn seit Ende 2020 auf insgesamt acht digitale Schneidsysteme von Zünd, vier Zünd Cutter L3 C-56 sowie zwei ältere Zünd Cutter LC-2400. Für den Zuschnitt von synthetischem und anderem Rollenmaterial hat Berkemann in einen Zünd Cutter G3 L-2500 investiert und in der Papiermodellabteilung kommt ein Zünd Cutter S3 M-1200 zum Einsatz.
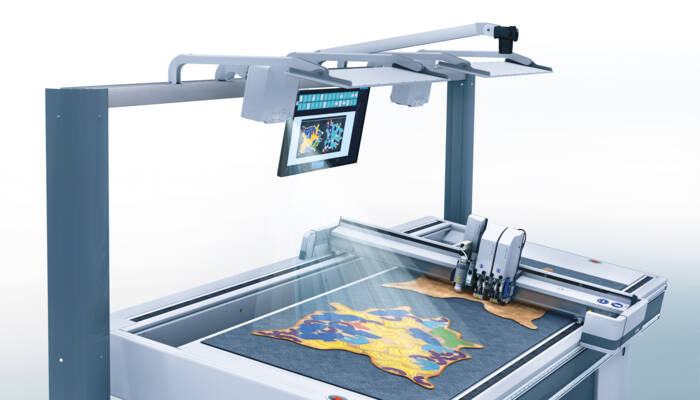
Einsparungen an allen Ecken
Das Einsparpotenzial eines digitalisierten Zuschnitts ist enorm. Das fängt bei den Stanzmessern an, die nicht mehr benötigt werden. Allein dadurch spart Berkemann jährlich rund 100'000 Euro an Bandstahl ein. Die Herstellung der Stanzmesser kostet aber auch Zeit. «Durch den Wegfall der Stanzmesser konnten wir unsere internen Abläufe um mehrere Wochen verkürzen. Wir müssen nicht mehr auf die Stanzmesser warten, sie nicht mehr einrichten usw. Sobald die CAD-Daten erstellt sind und ich mein Muster fertig habe, kann ich 1:1 in die Produktion gehen. Den ganzen Rattenschwanz an zusätzlichen Tätigkeiten und an zusätzlicher Kommunikation braucht es nicht mehr. Für ein Schuhmodell in verschiedenen Materialien mussten wir bisher bis zu drei verschiedene Stanzmesser- Sätze bestellen. Heute bewegen wir uns da rein virtuell und können Änderungen schnell und in letzter Minute vornehmen, ohne Werkzeugkosten ohne Zeit zu verlieren».

Scan-to-Order, der Workflow bringt auch Schuhherstellern Vorteile
Eine Eigenheit des Produktionsprozesses bei Berkemann ist der Scan-to-Order-Workflow. Dabei handelt es sich um einen Offline-Prozess, bei dem die Digitalisierung der Häute sowie die Verschachtelung der Schnittteile nicht auf dem Cutter, sondern über das Erfassungssystem MindCut Diva und die Mind-Software erfolgt. Die Aussendienstmitarbeitenden geben nach ihren Kundenbesuchen die Bestellungen auf ihren Laptops ein und übermitteln sie an die Zentrale in Thüringen. Im Rechenzentrum werden die Bestellungen gebündelt und an den Einkauf sowie das Supply Chain Management weitergeleitet. Dort wiederum wird die benötigte Materialmenge berechnet.
Die im CAD berechneten Ist-Flächen werden kalkulatorisch um verschiedene Zuschlagsfaktoren ergänzt. Auf diese Bruttofläche werden die verschiedenen Schuhteile angelegt – sofern es dasselbe Material in derselben Qualität und Güte ist – und aufsummiert. Und auf diese Weise kommt die für diese Order benötigte Flächenmenge zustande.
Ist die notwendige Ordermenge beisammen, geht’s in die Produktion. Produziert wird bei Berkemann ausschliesslich auftragsbezogen. Die Modellvielfalt ist enorm und eine Artikelbestellung kann auch mal bei 20 Paar liegen: «Wir sprechen dann aber eher von Musterfertigung als von individualisierter industrieller Fertigung. Wir müssen maximal flexibel und effizient arbeiten können. Aber auch höhere Volumina sind dabei, bis zu 2000 Paar von einem Artikel. Also zum Beispiel ein Schuhmodell in einer Farbe in 14 verschiedenen Grössen.»
Der Zuschneider geht dann mit seinem Lederbock ins Materiallager, scannt die Aufträge ein und stellt die Materialien entsprechend zusammen. Dabei wird auch gleich der zugehörige Schneidjob am Cutter vorbereitet. Der Bediener muss eigentlich nur noch mit einem Doppelklick bestätigen, die vorher mit einem Barcode versehene Haut auf den Tisch legen, ausrichten, die Markierungen anklicken und schon geht’s los mit dem Zuschnitt. «Ich weiss also über den Barcode, den ich auch über den Cutter einscanne, welche Haut ich vor mir liegen habe und bekomme dann automatisch das Nesting dazu sortiert. Auf gut Deutsch ein narrensicherer Prozess, der obendrauf noch Fehler vermeidet. Und ich erreiche eine sehr hohe Wiederholgenauigkeit.»
Mit dem Scan-to-Order-Workflow ist Berkemann viel flexibler geworden. Dadurch, dass sie unterschiedliche Modelle auf demselben Material nesten können, sind sie nochmals deutlich effektiver geworden. Und das alles auf Basis vorhandener CAD-Daten, die über den Model Importer fürs Nesting bereitgestellt werden. Damit nach dem Zuschnitt die Übersicht nicht verloren geht, werden die geschnittenen Teile verschiedenfarbig angeleuchtet. «Das Grossartige an der projektionsunterstützten Entnahme ist die Tatsache, dass wir die verschiedenen Grössen, aber auch die einzelnen Modellbestandteile, die wir ausschneiden, verschiedenfarbig anleuchten oder auch mittels Blinken hervorheben können. In der Praxis zeigt sich, dass wir in Zünd-Technologie investiert haben, die nach einem Jahr amortisiert war. Ich glaube, deutlicher kann man den Erfolg dieses Projektes nicht beschreiben.»
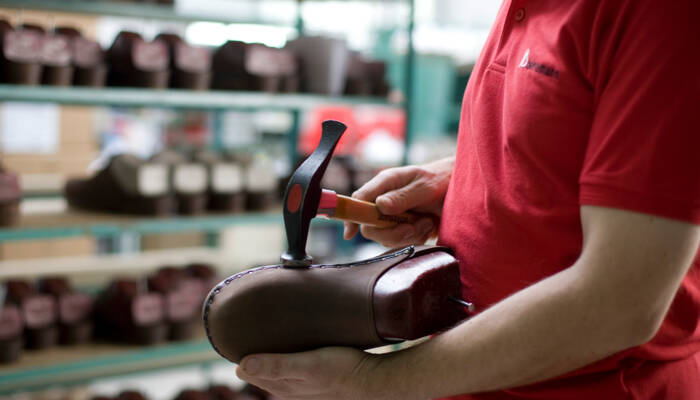