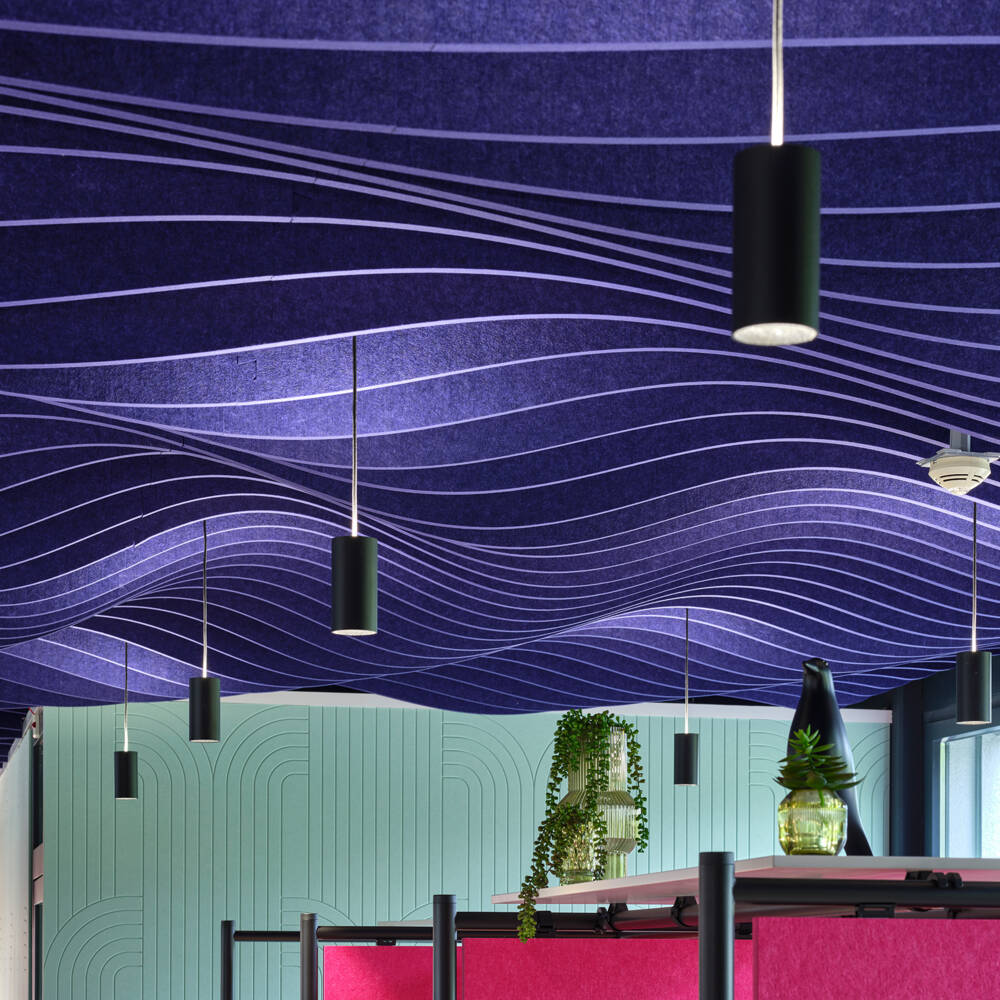
Digitaler Zuschnitt wirkt
Seit ihrer Gründung verfolgt Impact Acoustic eine klare Mission: hochwertige Akustiklösungen entwickeln und produzieren, die höchsten Ansprüchen der Nachhaltigkeit genügen. Dabei setzen sie auf Materialien wie recyceltes PET oder Zellulose und haben ihre Produktion von Beginn weg komplett digitalisiert. Ein Entschluss, der ohne Zünd und seine digitalen Cutter wohl nicht gefasst worden wäre. Und den die Verantwortlichen noch keinen Tag bereut haben.
Sie wollten einen Impact erzielen, etwas bewirken, bei dem Design und nachhaltige Entwicklungsziele einhergehen. Und sie wollten die Raumakustik verbessern und helfen, das Raumecho zu reduzieren. Mit diesem Anspruch gründeten Sven Erni und Jeffrey Ibañez 2019 die Impact Acoustic. Beide haben ihre Wurzeln in der Architektur und im Design und waren beruflich jahrelang in Asien und Europa unterwegs. Gemeinsam mit insgesamt rund 100 Mitarbeitenden entwickeln und produzieren sie heute in Luzern in der Schweiz Akustiklösungen für unterschiedlichste Einsatzzwecke. Für den Zuschnitt setzte Impact Acoustic von Anfang an auf Schneidtechnik von Zünd. Mittlerweile sind bereits drei Zünd Cutter G3 XL-3200 im Einsatz. Und sie haben gut zu tun. Die Akustikmaterialien werden im Schichtbetrieb zugeschnitten, die Auftragsbücher sind gut gefüllt. Mit der konsequent digitalisierten Fertigung kann die Nachfrage aber gut bewältigt werden. «Wo früher schlichte Metalldecken hingen, sind heute flexiblere Lösungen gefragt, die höheren Ansprüchen an Raumakustik und Ästhetik genügen müssen», erklärt Sven Erni. Die Kundschaft kommt hauptsächlich aus dem Office-Bereich und immer öfter auch aus Tourismus und Hotellerie.
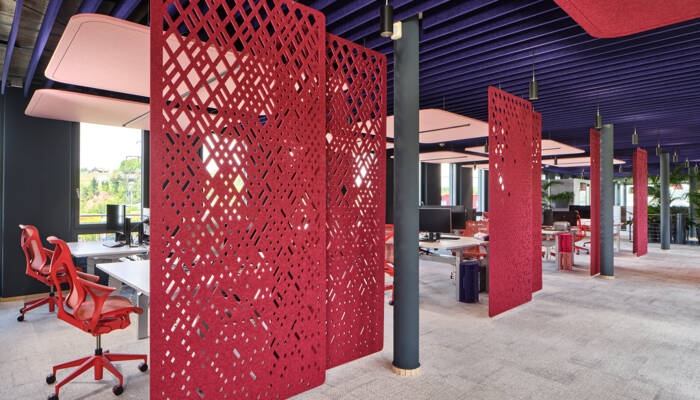
Impact Acoustic bedient auch im asiatischen Raum namhafte Kunden und hat mit Mitinhaber Jeffrey Ibañez, der aus den Philippinen stammt, quasi einen persönlichen Draht zu diesem Markt. Es lag deshalb fast auf der Hand, dass Impact Acoustic 2022 im philippinischen Biñan, rund eine Autostunde südlich von Manila, eine zweite Produktionsstätte aufbauten. «Wir bedienen von Biñan aus vor allem unsere wachsende Kundschaft im asiatischen und amerikanischen Raum. Der zusätzliche Standort ermöglicht es uns, lokaler und vor allen Dingen emissionsarmer produzieren zu können», erklärt Sven Erni. Auch wenn 10'000 km zwischen den beiden Standorten liegen, die Zusammenarbeit funktioniert reibungslos. Auftragserfassung, Produktentwicklung und Produktionsplanung werden grösstenteils über die Philippinen abgewickelt. Und für den Zuschnitt kommt auch in den Philippinen ein typengleicher Zünd G3 Cutter zum Einsatz. «In einer solchen Konstellation sind digitalisierte und standardisierte Prozesse ein absolutes Must. Wir haben hier wie dort dieselben Produktionsstandards etabliert.» Für das zentrale Monitoring ihrer Produktion an den beiden Standorten arbeitet Impact Acoustic mit Zünd Connect. Alle Zünd Cutter sind via Cloud eingebunden und liefern in Echtzeit Produktionskennzahlen. Dazu Sven Erni: «Wir unterscheiden produktionstechnisch nicht zwischen den Philippinen und der Schweiz. Wir können alle Cutter von Luzern aus überwachen und haben über verschiedene Dashboards alle relevanten Kennzahlen jederzeit im Blick. Demnächst eröffnen wir in Italien einen dritten Standort, was die Komplexität weiter erhöht». Die Daten aus Zünd Connect schaffen Transparenz und helfen Impact Acoustic, Optimierungspotenzial in ihrem Produktionsworkflow zu identifizieren.
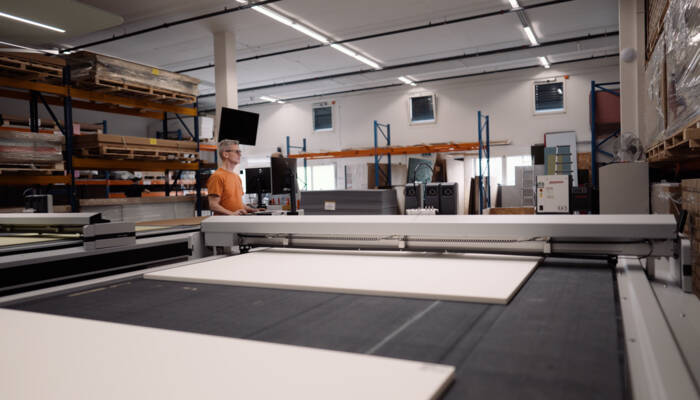
Nachhaltigkeit ist auch beim Material ein Must
Das Erfolgsrezept schlechthin und mindestens genau so wichtig wie der digitalisierte Zuschnitt ist das Ausgangsmaterial, das Impact Acoustic verwendet. Der Aspekt der Nachhaltigkeit, das Konzept des Upcyclings spielen dabei eine zentrale Rolle, der ökologische Fussabdruck soll so klein wie möglich gehalten werden. So wie jener des selbst entwickelten Archisonic Felt, einem «Hochleistungs-Akustikabsorber», einer umweltfreundlichen Akustiklösung, die aus recycelten Plastikflaschen hergestellt wird. In jedem Quadratmeter des Materials stecken 88 wiederverwertete Einwegflaschen. «Die Materialien, die wir verwenden, haben eine textile Charakteristik und sind nie völlig homogen und eben. Entsprechend akkurat und präzise muss der Zuschnitt sein, um unsere Qualitätsansprüche erfüllen zu können. Wo ein Schnitt beginnt oder aufhört, sehen Sie zum Beispiel nicht. Das klingt selbstverständlich, schliesslich geht es um geschlossene Formen, erstellt in einem CAD-Programm. Fakt ist allerdings, dass nur die Cutter von Zünd unsere hohen Anforderungen an Präzision und Qualität im Zuschnitt erfüllen kann».
Der neuste Wurf von Impact Acoustic ist Archisonic Cotton, ein Schallabsorber, der aus nachhaltiger Naturfaser hergestellt wird. Hauptbestandteil ist Zellulose aus sogenannter Baumwoll-Linters, einem Nebenprodukt aus der Baumwollindustrie. Das Material ist vollständig wiederverwendbar und die Absorber können am Ende ihres Lebenszyklus zu 100 % in den Produktionsprozess zurückgeführt werden. Dadurch wird der Abfall reduziert und gleichzeitig die begrenzten Ressourcen effizient genutzt.
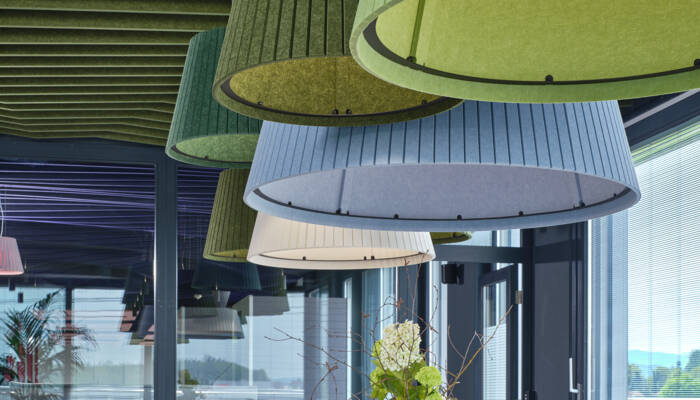
Es können auch mal ein paar tausend Quadratmeter sein
Schallabsorbierende Wandpaneele oder Trennwände, akustische Deckenplattensysteme oder individuell gestaltete Meetingboxen, die Bandbreite an akustischen Lösungen ist enorm. Impact Acoustic stellt sie alle von A bis Z selbst her, vom Ausgangsmaterial über das Design am Computer bis hin zur Montage vor Ort. Aufwendige Projekte wie beispielsweise Akustikprojekte für Grossraumbüros, die sich über mehrere Etagen erstrecken, können gut und gerne mehrere 1000 m2 «gross» sein. «Solche Aufträge bestehen schnell einmal 30'000 Einzelteile.» Und jedes ist wieder etwas anders als das andere. Hier die Übersicht zu behalten, ist nur mit detaillierten Produktions- und Montageplänen möglich. «Auf jedes einzelne Teil werden noch während des Zuschnitts alle relevanten Auftrags- und Positionsdaten aufgedruckt. Das erleichtert den Monteuren vor Ort die Arbeit, da sie anhand er Montagepläne exakt wissen, welches Teil an welchem Ort montiert werden muss.» Nicht minder wichtig ist die Produktionsplanung für den Zuschnitt. «Die Monteure wären wenig begeistert, wenn Teil 3735 in derselben Liefercharge wäre wie Teil 5. Mit der entsprechenden Produktionssoftware von Zünd können wir sicherstellen, dass so etwas nicht passiert».
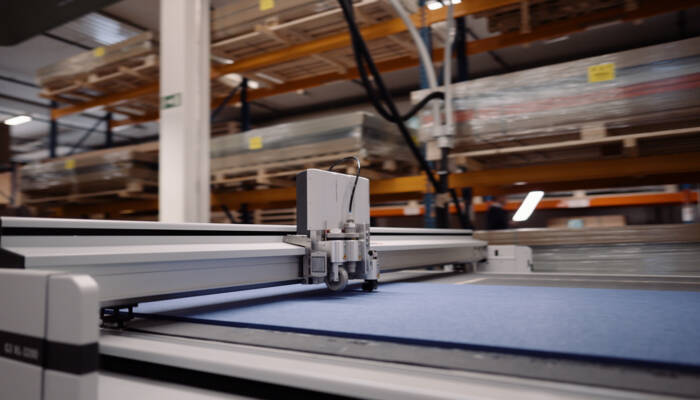
Ein kleiner Schritt vom Prototypen bis zum Serienprodukt
Die Kombination aus modernster Technologie, hochpräziser Schneidtechnologie von Zünd, erfahrenen Produktdesignern und Anwendungsingenieuren – Impact Acoustic hat alles, was es braucht, um Prototypen in ein greifbares, funktionierendes Serienprodukt zu verwandeln. Das Prototyping ist denn auch ein wichtiger Bereich bei Impact Acoustic. Von Losgrösse 1 bis Massenproduktion wird bei Impact Acoustic alles hergestellt. Einzelanfertigung genauso wie ein Prototyp, von dem anschliessend vielleicht direkt 50 oder 100 Teile hergestellt werden. «Auch hier können die Zünd Cutter die Vorteile eines digitalen Zuschnitts voll ausspielen. Wir sind sehr flexibel im Zuschnitt und können jeden Auftrag zuverlässig und pünktlich ausliefern.»
«Die Zuverlässigkeit der Zünd Cutter ist für uns zentral, besonders an unserem relativ kleinen Standort hier in Luzern. Unsere Zünd Cutter sind 24/5 im Einsatz und wir brauchen den Output. Würde ein Cutter auch nur für einen halben Tag stillstehen, hätten wir in unserer eng getakteten Produktionsplanung schnell ein Problem. Und ich kann auch dem Service von Zünd ein Kränzchen winden. Diese Flexibilität, Schnelligkeit und Kompetenz sind ausserordentlich. Das gibt uns ein sehr gutes Gefühl und ist ein wichtiger Grund, warum wir auf Zünd setzen.»
Digitaler Zuschnitt wirkt
Sven Erni und Jeffrey Ibañez gründeten die Impact Acoustic, um mit nachhaltigem Design die Raumakustik zu revolutionieren. Herzstück ihrer konsequent digitalisieren Produktion sind drei Zünd G3 Cutter. Sie bieten ihnen die Flexibilität und Präzision im Zuschnitt, die sie in der Herstellung ihrer Akustiklösungen benötigen.