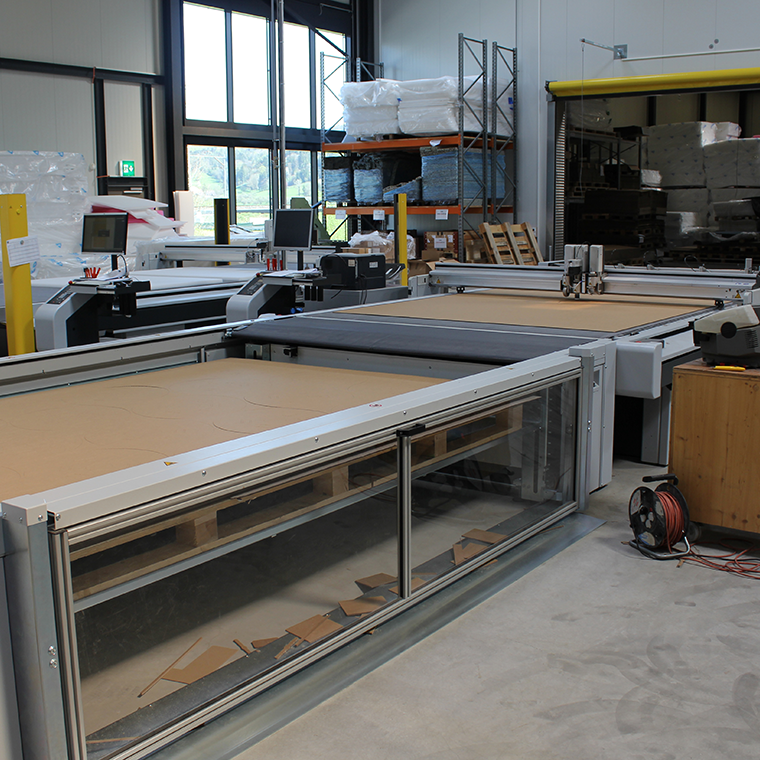
Fully automated digital cutting, perfectly packaged
Heer AG designs and develops custom packaging solutions in a production workflow geared towards maximum efficiency. There is a systematic strategy behind the Swiss packaging manufacturer's success. With its investment in a highly automated Zünd BHS150 Board Handling System, Heer has secured a competitive edge in packaging production at an industrial level.
In Switzerland and beyond, the B. Heer name stands for smart, customized packaging solutions. At the company's six locations, everything revolves around the development, production, and logistics of packaging, primarily for industrial customers. Heer packaging protects coffee machines, sensitive measuring instruments or laboratory analysis equipment during transport and usually consists of a combination of corrugated cardboard, foam, and wood. The foam ensures a secure fit in the cardboard box and at the same time provides protection against impact. Ultimately, maximum transport safety is what system packaging is all about. This is what is being manufactured at the Felben-Wellhausen location, where the company's Center for Corrugated Board and System Packaging has been housed since 2015. This is also where one can find two Zünd G3 cutters in continuous operation. With the investment in a highly automated cutting system consisting of a Zünd D3 cutter with BHS150 board handling, a third production line was added not long ago. For Joachim Basler, head of the Corrugated Center, the high-level automation and superior performance of Zünd production equipment are the two most important factors in meeting the requirements of their increasingly demanding customer base.
Because customers are placing orders in ever smaller quantities. At the same time, they continue to shrink their packaging inventory or forego keeping stock altogether. As a result, replacement cycles are becoming ever shorter. Furthermore, packaging is becoming more and more customized in order to ensure perfect protection of packaged goods. For Heer to be able to meet these demands, the company is always looking to optimize process efficiencies. In concrete terms, this means minimizing set-up and changeover times, automating production, and expanding to lights-out manufacturing. How this works can be seen in the sprawling production hall, where three Zünd cutting systems are in continuous operation, processing corrugated cardboard and packaging foams nonstop.
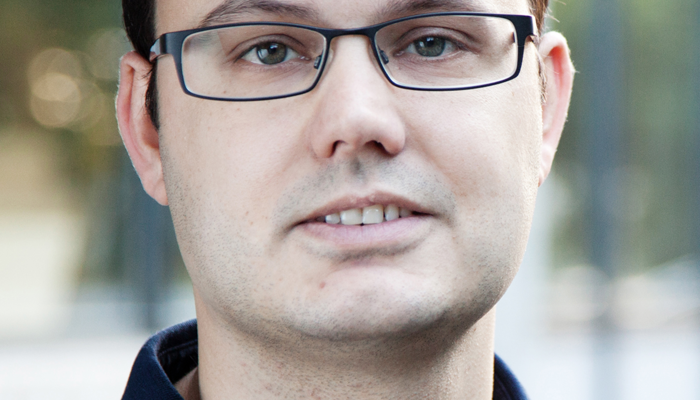
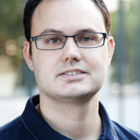
Heer's most recent addition was a state-of-the-art, fully automated material-handling system—the Zünd BHS150. The 1.5 m max. stack height and industrial-level automation that characterize the system are truly unique. "Thanks to the 1.5 m stack height, we can now drive entire pallets of raw material into the loading unit from which the boards are fed automatically. This means we have to put very little effort into the handling of raw materials and do not have to re-stack at any point. In addition, we can now also produce medium and long runs completely automatically, either during the day or at night. This significantly extends machine run time and helps reduce our production costs».
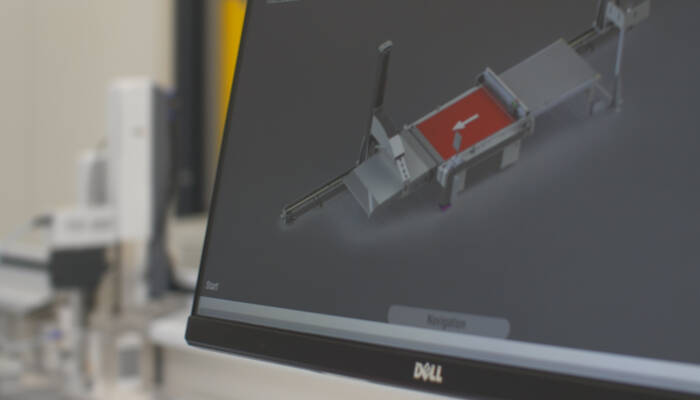
The innovative off-load unit with conveyor belt allows for bridge-free cutting of corrugated board. This increases efficiency even further. "Because of this feature, the time it takes to break out the cut pieces and separate them from the waste is much shorter. Without the need to add bridges, the cutting time itself is reduced, which in turn minimizes overall production time. And finally, without those visible connection points, the quality of the end product is greater as well.»
With the Zünd BHS150 Board Handling System, Heer is exploiting the full potential of fully automated production. The extended stack height of 1.5 m, combined with high processing performance and short setup times, leads to significant increases in productivity and profitability. The complete production line consists of a loading unit, a Zünd dual-beam D3 cutter, and an off-load system. The 1.5 m stack height allows for significantly longer operating time without interruption. As a result, even long runs can be finished economically and efficiently.