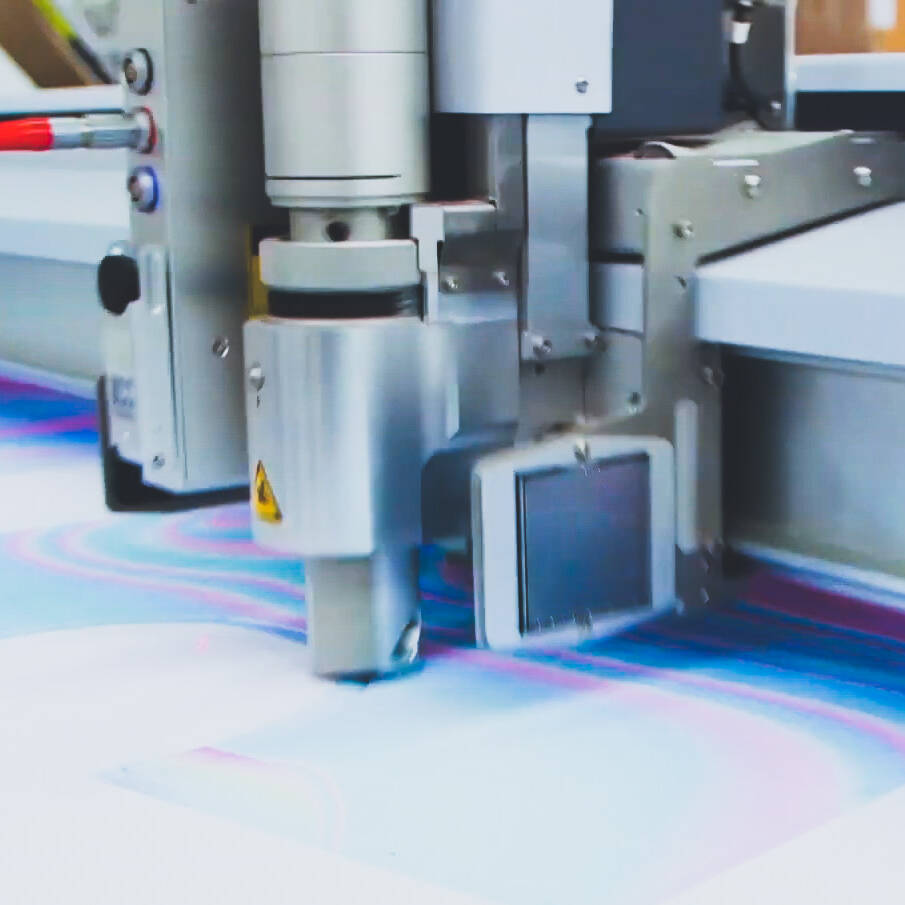
Smart factory, intelligent cutting technology
In 2019 Victor and Michal Tracz embark on a digital transformation of their family business, transitioning away from conventional textile finishing which had been profitable for a very long time. Times had changed though, especially in the textile industry, where their father had been active for 40 years. Print Logistic is one of the first adopters of the micro-factory concept in Poland. And for their digital cutting solution, they came to Zünd.
In 2019 Victor and Michal Tracz embark on a digital transformation of their family business, transitioning away from conventional textile finishing which had been profitable for a very long time. Times had changed though, especially in the textile industry, where their father had been active for 40 years. Print Logistic is one of the first adopters of the micro-factory concept in Poland. And for their digital cutting solution, they came to Zünd.
Micro factory – "the next big thing"
For Print Logistic, the solution presented itself in web-to-print, a market in which fully automated digital production systems are key to driving growth. In the garment industry, fully integrated, intelligent production cells, so called micro factories, began to form. Victor and Michal saw the potential and began building their own micro factory, one of the first such efforts in Poland. Tracz says: "It quickly became clear to us that custom garment fabric would be the next big thing." They developed their own print-on-demand solution, which is now connected with online shops of major providers across Europe. They do not, however, offer their own customer portal. A joint venture with an investor they were able to convince of their micro-factory idea gave them an additional boost. The plan to no longer just print finished textiles delivered to them but to bring the entire production process in-house was put into practice.
Michal Tracz isn't crazy about the micro-factory designation. Instead, he prefers to call it a "smart factory". Which is what it is... smart and intelligent. In his opinion, "micro" makes it sound too small scale, too inconsequential. And the concept of "small" hardly applies to anything in their operation besides, perhaps, production quantities per job. The intelligence lies in the production process as a whole, he explains: “In conventional garment manufacturing, individual production processes are outsourced to different companies. Those are often far away and entail lengthy delivery routes, which make profits possible only when it comes to very high volumes. For us, smart means bringing every part of production back in-house so we can cover the entire value chain."
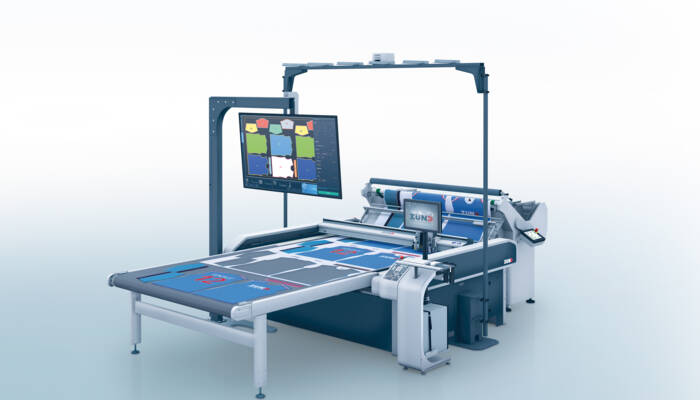
Digital cutting, a key component of the smart factory
Print Logistic can now produce thousands of personalized items of clothing in less than 72 hours from receiving an order. “To be able to do this, we need smart production methods—digital cutting, digital printing, direct-to-garment, roll to roll." Digital cutting is a central component of the smart factory. “It accounts for 33% of our success, while digital printing and sewing each contribute another third". In a smart factory, printing, cutting, sewing, and logistics mesh together like well-oiled gears. Without digital cutting, our production workflow would not be possible at all: “Every piece of clothing is customized. In order to be profitable, we must have very short lead times; that is absolutely key." And speed goes beyond mere cutting. It involves the cutting speed of the Zünd S3 as well as job retrieval via barcode scan and short setup times. “The fact that the Zünd cutter is so fast and efficient is also due to its high level of automation and the clever solutions for material feeding as well as parts removal. Customers expect products ordered online to be in their mailbox within three to five days. This is possible only with a production workflow that is extremely lean and highly automated."
"Beyond such technical considerations, we are also very satisfied with our investment in Zünd digital cutting technology from an economic point of view." The job is by no means done simply by establishing a smart factory. It presents challenges on many levels. The ability to deliver consistently high quality without losing sight of margins is a constant concern. There is still a lot of potential for further automation in sub-processes. "The well is far from running dry."
Sustainably reliable
Tracz sees perhaps the greatest advantage of the smart factory in its sustainability: “We don't tie up any capital in extensive warehousing, we don't have to throw away any unsold inventory. Digital cutting with the Zünd S3 Cutter gives us perfect material yield with very little waste". In Poland Print Logistic is considered a pioneer in establishing a digital textile micro factory. But there's always a price to pay when you're the pioneer. It was no different for Tracz and his brother. Which is why they are all too familiar with the potential stumbling blocks: first and foremost are the delivery times that must be kept; then there are the complexities of the entire production process and the software needed to manage it all. Since there was no single software product available to control the process in its entirety, they simply proceeded to programming it themselves. And while they were at it, also developed a 3D customizer.
For Michal Tracz, an important key to success was choosing the right hardware. Production equipment that can be integrated seamlessly. Systems like Zünd offers, with the flexibility and reliability necessary for cutting hundreds of parts for different garments on a daily basis, with precision, and as part of an automated workflow. "With Zünd, we also opted for a cutting system able to cope with a wide variety of materials without compromising on performance or cut quality". Cotton, linen, rayon stretch fabrics, bamboo fabrics – as diverse as the properties are of all these different textiles, so are their processing methods. Says Tracz: "These fabrics all differ in the way they unwind from rolls, and during the cutting process, we have to be able to reliably compensate for any shrinkage and stretch." It's easy to tell that Zünd has a lot of experience in cutting textiles. "Our verdict, one and a half years after making our purchasing decision, is positive through and through:" We began this venture a year and a half ago and relied on digital cutting technology from Zünd right from the start. In that entire time, we have not experienced a single machine breakdown or any other problem with our cutter. We couldn't have been any more correct in counting on the legendary reliability and quality of Zünd digital cutting systems."
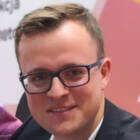