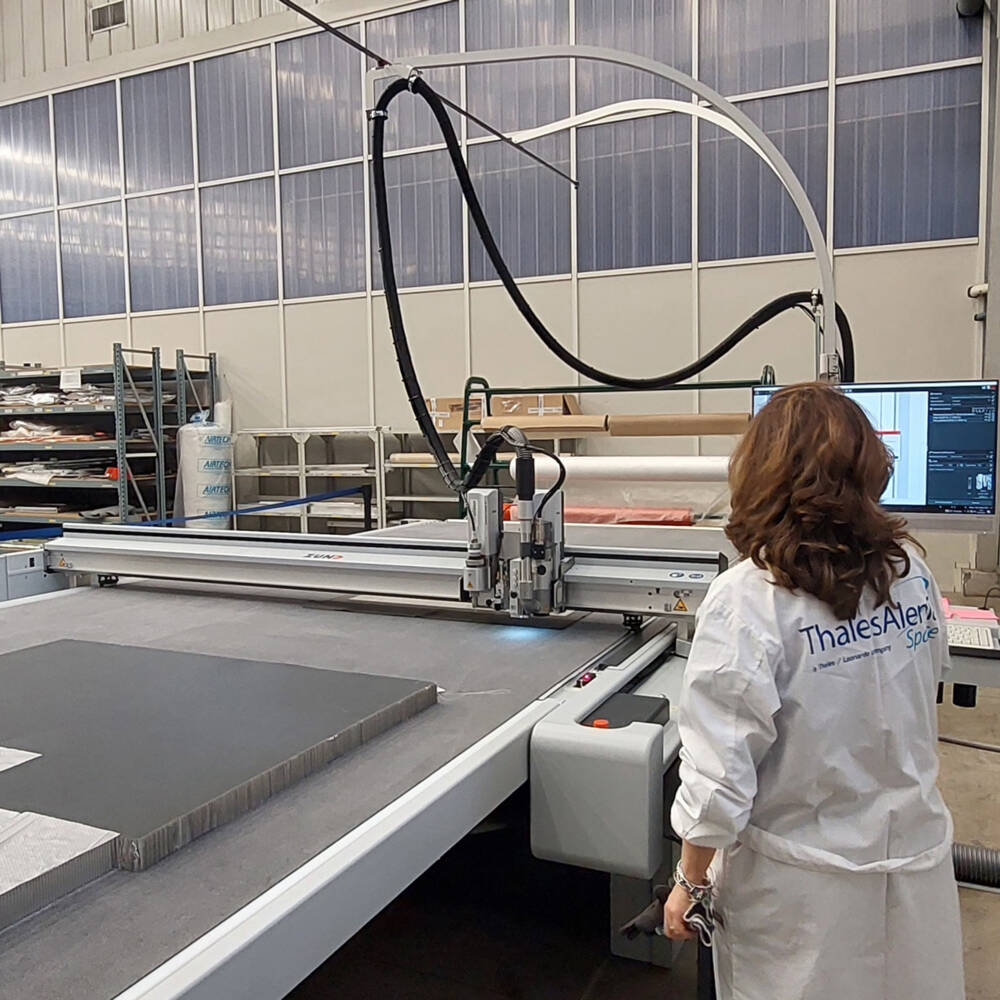
Zünd goes to Space with Thales Alenia Space
Thales of Miletus, Greek philosopher of the VII b.C, was the first to formulate theories on space and the universe, earning the anachronistic title of "astronomer". From the time of Thales to today, the sector has made great strides and man has not limited himself to theorizing about Space but has also begun to explore it.
Zund Italia met Thales Alenia Space in Turin which, in addition to recalling Thales in its company name, has been a leader in the field of Telecommunications, Navigation, Earth Observation, Exploration, Science, and Orbital Infrastructures for over 40 years. The Galileo satellite navigation system, the COSMO-SkyMed dual observation system, and the Orion-MPCV spacecraft are among the best-known projects, but not the only ones, in which Thales Alenia Space is the protagonist, in synergy with ESA (European Space Agency) and NASA (National Aeronautics and Space Administration). "Speaking specifically of Orion-MPCV" explains Tiziano Pegorin, Head of the Italian Structures Competence Center "The "Made in Thales Alenia Space" components are the structure and the thermal control of the MPCV service module of the ORION capsule, which houses the engine of the vehicle and mission support systems such as fuel supplies, water supplies, radiators for system cooling and solar panels for power generation".
The backbone of the service modules, Thales Alenia Space's core business, often includes structures made of composite materials which, during the manufacturing phase, must be cut to size, with precision in the order of a tenth of a millimeter.
And this is where Zünd came into play with its highly productive automatic digital cutting solutions, capable of processing a wide variety of materials, among which composites stand out.
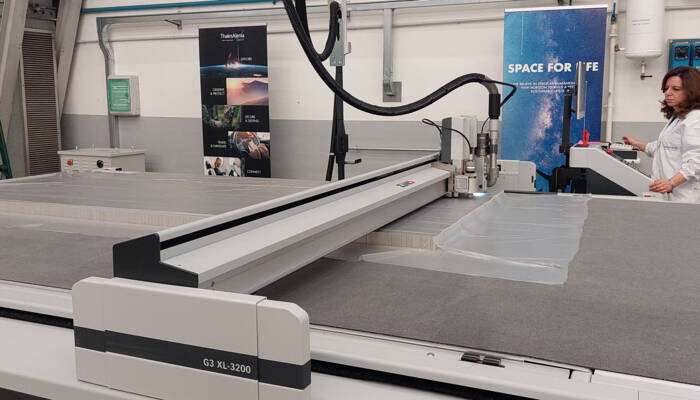
More efficiency and productivity with Zünd
In the Turin plant, where the structure of satellites and space vehicles is designed and built, the cutting of composite materials, before the advent of Zünd, was outsourced.
In the world in which Thales Alenia Space operates, however, the time between the engineering definition and the need to create the parts is even shorter. Accuracy and quality of the final product are also essential characteristics. Involving external companies in the design and construction phase caused unsustainable logistical-bureaucratic problems and delays and there was no direct control of the activities. In order to optimize the manufacturing processes, in particular of the panels for the satellite structures, the production is rethought, including the material cutting phase. "It was decided to bring in-house the phases that were outsourced, including cutting, and which had a considerable impact on the overall timing" explains Roberto Milani, Head of Officine Strutture.
Zünd cutters are strategic allies for all companies that need to make production more efficient, with a view to lean manufacturing and "just in time", without neglecting flexibility, precision, and quality, the latter characteristics being basic for all sectors, but even more so in the aerospace sector.
The Thales Alenia Space project envisaged the installation of G3 XL-3200, with piece collection table and Carbon Fiber Protection, i.e. a shielding system supplied by Zünd for the specific composite sector which helps to preserve the electrical components from potential short circuits caused by carbon fiber filaments. The machine is equipped with an initialization system (Integrated Tool Initialization - ITI) which allows automatic adjustment of the machining depth of each type of tool, for increasingly precise and rapid execution of cutting operations. The G3 model is extremely versatile and modular. Depending on the material in the machine, you can choose between different tools, such as the Pneumatic Oscillating Tool - POT, more suitable for honeycomb and considerable thicknesses; the Universal Cutting Tool- UCT, with a fixed tangential blade, for very rapid cutting of thinner thicknesses. Thales Alenia Space has also installed the Routing Module - RM-A, a 1 kW cutter, useful for processing materials such as honeycomb, aluminum, and ablatives. Andrea Giannitti, Head of Composite Material Technologies and Processes, draws attention to the possibility of having a library of materials that provide a set of suggested cutting settings and, at the same time, customizable according to one's needs. "At Thales Alenia Space, every process is certified. With Zünd, we insert these "recipes" into the system and operators can access them quickly and in total autonomy, repeating the same process, without the risk of errors" explains Giannitti.
Roberta Minore, Cutting Operator, enthusiastically talks about her experience of using Zünd "It's a complete cutting machine, but at the same time user-friendly. Working with Zünd is really gratifying". Minore emphasizes the possibility of perfecting cutting methods according to your needs, choosing from the wide range of tools in the Zünd catalog. Another advantage highlighted by Minora lies in the possibility of creating nesting autonomously, based on the scraps, while the machine is completing a job, with a consequent reduction in downtime.
Thales Alenia Space has equipped the machine with an ICC (Integrated Compact Colour) camera thanks to which it is possible to automatically detect and follow the selvage before cutting and, in the event of irregular edges, allows to avoid producing pieces that would otherwise be incomplete and waste a lot of raw material.
Thales Alenia Space's G3 has the requisites to be included in the "Industry 4.0" plan. It is equipped with the Cut Queue software, an optional component that allows you to simplify the workflow, create a job queue, introduce some automation, and at the same time provide some useful reports to improve production performance.
"The machine was recently installed and we are discovering its potential day by day. Certainly, having data available relating to the wear of consumables and production efficiency is useful for introducing improvements in processes and for statistical purposes, but also to guarantee the final product through certifications" specifies Milani.
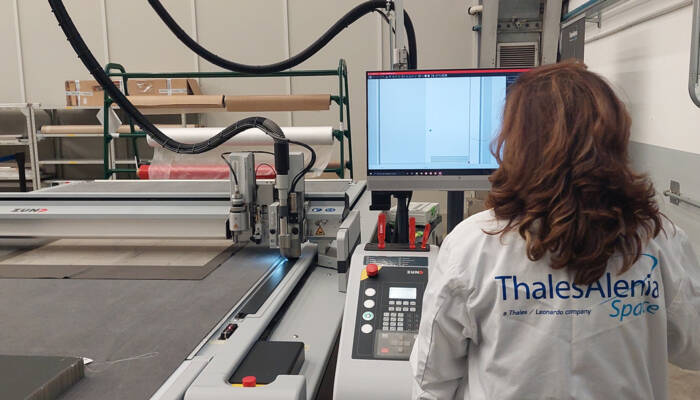
Why Zünd?
Thales Alenia Space was familiar with the quality of Zünd cutting machines, which have been in operation for several years in the French Thalés plant in Cannes. The proven reliability and the advantage of having identical means of production in the various locations, in order to ensure synergy in processes and facilitate the transfer of know-how between operators, were already sufficient reasons for choosing Zünd. "The positive experience in France certainly influenced the choice for the Turin plant" admits Milani "But what convinced us was the proven versatility of the machine". The practical and operational benefits have exceeded all expectations.
Some practical examples: Thales Alenia Space jumpers and space modules are characterized by a light and at the same time resistant structure, with a minimum mass. To achieve this result, Thales Alenia Space uses so-called sandwich panels, made up of two composite or aluminum laminates separated by honeycomb. Thanks to Zünd, it was possible to reduce waste and extra machining following the increase in precision in cutting aluminum honeycomb. In addition, lead times for cutting aluminum sheet metal for flight parts or equipment have shrunk significantly.
The most recent application of the Zünd machine, where the advantages of automatic cutting were immediately clear and evident, is linked to the Mars Sample Return mission in collaboration with ESA. The mission will bring a satellite into the correct orbit of Mars with the aim of taking material samples. The central element of the satellite, under construction at Thales Alenia Space, consists of a truncated cone in carbon fiber externally and sandwich panels internally. The truncated cone shape implies that, in order to maintain the correct orientation of the fibers, the outer covering is composed of various sections joined side by side. With a manual cut, the creation and optimal yield of this coating would have been much more expensive and complex. Thanks to Zünd, it has been possible to increase the speed in the preparation of cut kits of carbon fiber prepreg for lamination, especially for curved components. "We experiment almost daily with new cutting solutions, on as many materials. We recently experimented with cutting natural cork for re-entry vehicle upholstery. Again, the result was in line with our needs".
High-quality standards and proximity to customers are the goals that Zünd pursues in Italy and around the world. "Made in Swiss" is a guarantee of extremely reliable and long-lasting production systems, but this is also accompanied by rigorous and reliable customer service that Zund Italia takes care of at every stage, from site inspection to installation and after-sales. The professionalism and courtesy of the Zund Italia technical team were recognized by Pegorin and Milani during the supervision of the machine installation works.
- In short, Zünd can proudly state it: mission accomplished!
Who is Thales Alenia Space?
With over forty years of experience and a unique set of skills, expertise, and cultures, Thales Alenia Space offers cost-effective solutions in the fields of Telecommunications, Navigation, Earth Observation, Environmental Management, Exploration, Science, and Orbital Infrastructures. Both private and governmental industry count on Thales Alenia Space to design satellite systems that provide connection and positioning anywhere and everywhere, monitoring our planet, enhancing the management of its resources, and exploring our Solar System and beyond. Thales Alenia Space considers space as a new horizon, which allows life on Earth to be improved and made more sustainable. A joint venture between Thales (67%) and Leonardo (33%), Thales Alenia Space together with Telespazio also forms the strategic partnership "Space Alliance", capable of offering a complete set of services. In 2021, the company achieved a consolidated turnover of approximately 2.15 billion euros. Thales Alenia Space has approximately 8,900 employees in 10 countries, at 17 sites in Europe, and one plant in the United States.
Thales Alenia Space in Italy has approximately 2,300 employees in 4 plants: Rome, Turin, Milan, and L'Aquila.
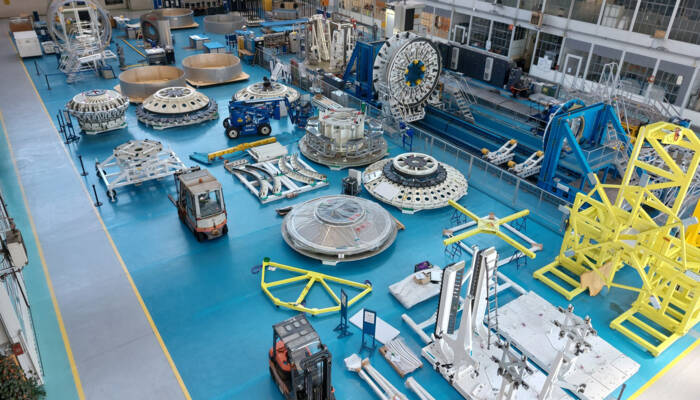