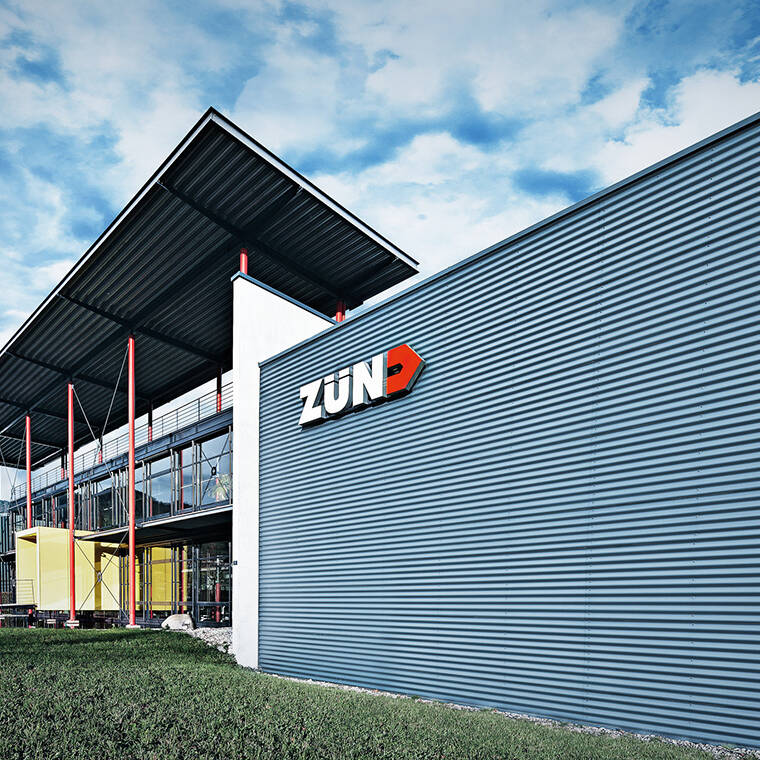
Back to overview
News
We're keeping you up to date! Here you will find all the news from the world of Zünd, exciting user stories, and relevant information on upcoming trade shows where you can see Zünd cutters in action.
Newsletter
Sign up for our newsletter and receive up-to-date information on trade shows and other Zünd news.
15 Events found
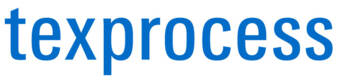
23. April 2024 - 26. April 2024
Texprocess
Messe Frankfurt, GER
Hall 8.0 / Stand C89
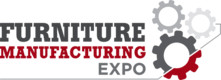
13. June 2024 - 14. June 2024
Furniture Manufacturing Expo
Hickory, North Carolina, USA
Hall / Booth #1305
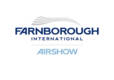
22. July 2024 - 26. July 2024
Farnborough International
Show Centre, Farnborough, UK
Hall / Stand Composite UK Pavilion Stand (Pod 21)
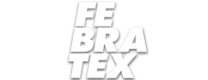
20. August 2024 - 23. August 2024
Febratex
Blumenau - SC Brazil
Stand 127/129 Sector 02
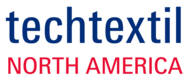
20. August 2024 - 22. August 2024
Techtextil North America
Raleigh, North Carolina, USA
Hall/Booth #1201

9. September 2024 - 12. September 2024
CamX
San Diego, CA USA
Hall / Booth #LL25
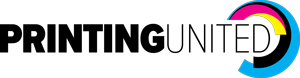
10. September 2024 - 12. September 2024
Printing United
Las Vegas, NV USA
Hall / Stand: #C1161
Schedule a live demonstration
Schedule a personal demonstration. Experience live how our digital cutting solutions help increase productivity and efficiency.
Schedule a live demonstration